文/熊宇翔 编辑/罗松松
来源:远川商业评论
2009年,轰轰烈烈的新能源汽车补贴拉开大幕,资本市场看到了一个全新产业的机会,但负责此事的时任工信部副部长苗圩眼里却全是挑战。在次年1月的北大光华新年论坛上,苗部长语重心长:“最大的问题是电池,电池最大的问题是占30%左右成本的隔膜,这种隔膜我们一家都做不了[1]”。
顾名思义,隔膜的作用是分隔正极和负极,避免电池短路。它的原材料分为聚乙烯(PE),聚丙烯(PP),前者主要用于三元锂电池,后者多用于磷酸铁锂电池,它的存在直接决定了电池安全、能量密度、充放电倍率以及循环寿命等指标。2017年三星note7爆炸,便是因设计问题导致隔膜受损。而今年通用召回14万辆电动汽车,原因也指向了电池隔膜起皱。
但十多年前,中国人对这张细如发丝又无比重要的塑料膜无计可施,只能有求于欧美和日本。日本厂商要求提前45天打款,并且还会审查资质,禁止中国进口用于军事用途。
隔膜有如此强的卡脖子能力,在于几个特点:
第一,它属于绝对的技术密集型,自动化水平极高,不可能上演徒手拉膜的神技,因此中国的人口红利派不上多大用场;其次,资金门槛高,在中国隔膜产业刚起步的2006年,仅一条湿法产线投资就2000万元起步;除此之外,供应链认证周期长,国内为一年,国外长达两年,待到大规模供货,三、四年就过去了,但中国中小企业平均寿命都不到三年。
然而,随着中国新能源汽车产业的崛起,锂电产业链实现了全面国产替代,隔膜也不例外。2020年,全球锂电池隔膜出货62.8亿平米,中国出货38.7亿平米,产量占比61.6%,催生了一批小巨头,包括拿下全球20%市场,市值超过2500亿的恩捷股份。
通过对隔膜行业和恩捷的回溯,我们试图回答三个问题:
1. 隔膜产业变迁背后的根本原因是什么?
2. 恩捷为什么能成为全球电池隔膜龙头?
3. 隔膜的下一个战场在哪里?
无形的手
纵观过去三十年,全球锂电产业每次变迁背后都离不开一只无形的手:终端,下游终端产品的变化直接影响上游供应链的产业格局,隔膜是一个典型。
1. 从消费电子到电动车
2010年之前,锂电池主要用在定位器、笔记本电脑和MP3等3C产品上,日本三洋、松下、索尼、日立等少数公司凭借下先发优势和技术实力占据了50%的市场。在隔膜领域,日本更是一家独大,一直到2013年,全球市场份额稳定在5成以上。
中国虽然从上世纪90年代开始研究隔膜,但第一批企业出现已经是2003年前后的事,2009年左右才开始出货,8成以上都需要进口,一直到2011年,国内隔膜的出货量只有0.98亿平方米,市场规模只有5.4亿元。
当时,隔膜主要用于消费电子领域,不过一部定位器只需一块电池,一部笔记本电脑需要六块,但是一部续航400公里以上的电动车至少需要上千块,对隔膜的需求和3C不在一个级别。尽管2010年中国新能源汽车销量尚不到2万辆,但一个巨大的风口已经近在眼前。
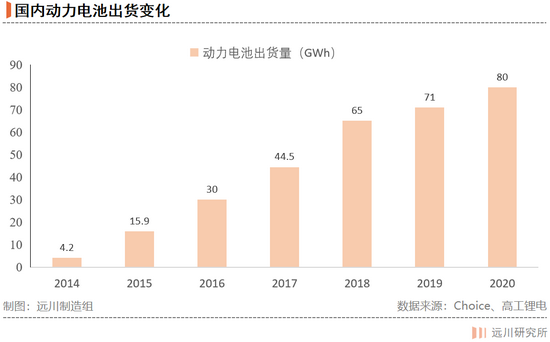
2015年,在新一轮的巨额补贴***之下,中国新能源汽车销量暴增近4倍达到33万辆,超越美国成为全球最大的新能源汽车产销国,动力电池出货量达到15.7GWh,迸发的国产替代需求带着国内隔膜产业开始起飞。当年隔膜国产化率提升到45.5%,出货量提升到6.28亿平米。
锂电池下游应用从3C电池向动力电池的加速转移,为国产隔膜的产业升级提供了一个巨大的舞台。
2. 从干法为主到湿法为主
隔膜的主要技术路线分为干法、湿法,前者工艺更简单、成本低、耐高温安全性好,但更厚更重,会拉低电池能量密度,所以更契合磷酸铁锂电池;后者工艺复杂、成本高、耐热性稍差,但较轻薄,能提升能量密度,因此主要用于三元锂电池。
国内绝大多数隔膜企业早期选择了成本较低、更易上手的干法路线,也符合当时下游的主流需求——从2010年到2016年,磷酸铁锂因为其安全性优势被车企优先采用,出货量一直力压三元锂。但当时磷酸铁锂不耐冻、能量密度低的问题未能解决,占新能源汽车销售大头的乘用车在逐渐倒向三元锂,湿法隔膜的市占率其实已经在逐年走高。
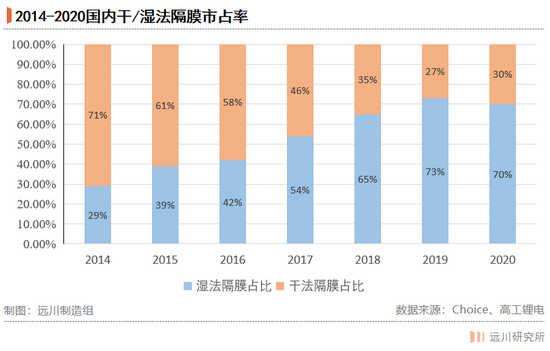
而2016年末,政府出台了新的补贴政策,将电池能量密度纳入考核标准,一举将三元锂电池送上快车道,也让湿法隔膜反超干法成为主流技术。湿法隔膜工艺比干法更复杂,但售价也更高。这次技术路线切换,为国产隔膜提供了一个量价齐升的超车机会,一批有竞争力的隔膜企业脱颖而出,冲向了原本被日本占据的价值高地。
2015年,世界排名第一的日本旭化成为应对竞争,收购世界第二的美国Celgard,组成了一支全球市占率36%的银河战舰,但依然未能挡住中国的前进步伐。2018年,旭化成第一次丢掉了世界第一的宝座,接替者正是恩捷股份。
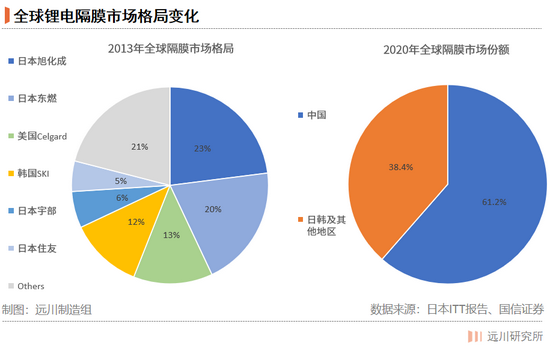
国产逆袭
2010年,上海恩捷在浦东成立,8年之后就取代前任世界霸主。在制造业这样的速度超乎想象,但在剧变的锂电产业中则合情合理。隔膜企业的兴替,直接取决于下游电池厂的选择与业绩。火车跑得快,全凭车头带,而恩捷的火车头是开了挂的宁德时代。
2015年,恩捷成为宁德时代的隔膜供应商。2015年-2020年,宁德时代动力电池出货量翻了20倍,从2.52GWh增长到51.71GWh。恩捷的隔膜销量则涨了30倍还多,从0.41亿平米增加到13亿平米。
能搭上宁德时代这班车,恩捷的过往积累与技术路线选择起了关键作用。
恩捷的创办者李晓明、李晓华兄弟大概是行业里专业最对口的企业家——他们从马萨诸塞大学高分子材料专业硕士毕业后,在美国塑料包装公司工作,1996年回国创业。两人先创办的“云南恩捷新材料”主营BOPP膜、香烟包装膜等传统产品,公司营收达上亿规模。因为生产BOPP膜的设备与工艺和隔膜相仿,两人又创办了上海恩捷生产湿法隔膜。
因为有云南恩捷的积累,上海恩捷的创业过程,其实是踩在兄弟公司肩上的高举高打,资金、工艺经验、技术人才兼备。同时,恩捷成立便全力押注湿法隔膜,又预判了下游的需求。
上海恩捷成立后,从日本制钢所进口了一条隔膜生产线,后者1958年进入隔膜制造设备行业,产品以稳定、品质好、能耗低著称,每年供应有限,需要提前预订。
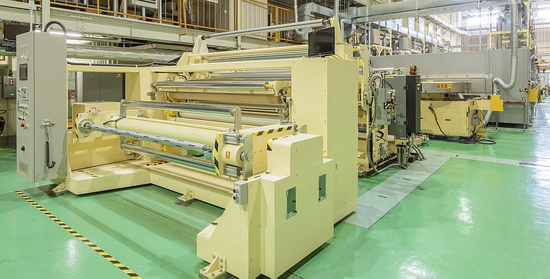
买来容易转起来难。恩捷调试了三年,才开始有产品产出,但这已属不易。南洋科技(已更名航天彩虹)2012年花1500万欧元从德国购买一条隔膜产线,调试了8年多也没成功量产,今年含泪将产线挂牌转让。[3]
恩捷则在先进设备和工艺积累加持下,湿法隔膜很快达到国外主流水准,在度过产能与良率爬坡期后,2015年打入了国内外电池大厂的供应链,尤其是当时力推三元锂,对湿法隔膜需求大增的宁德时代,命运由此改写。
国内最早成立的隔膜企业星源材质,那时则在据守干法,大客户是比亚迪与LG,直到2018年才挤入宁德时代供应链,起个大早赶个晚集。
选对技术,找对客户,是隔膜新龙头崛起的必要条件,但并不充分。归根结底,隔膜的竞争还是制造业的内里——扩产能,降成本,将规模效应发挥到极致。
恩捷在2014年市占率不足1%,远不如星源材质、中科科技等公司,即便是到2016年也没有和竞争对手拉开太大差距, 市场份额只比星源材质多0.2个百分点。但正是在这一年,恩捷开启了倍增式产能扩张。
2017年,恩捷在珠海的12条产线开工,2018年产线贯通后,恩捷的名义产能从3亿平米提升至13亿平米。这对恩捷来说,绝对是一场豪赌。因为在2018-2019年,中国新能源汽车销量因为补贴退坡等原因首度负增长,恩捷的股价也一路震荡向下,从2017年年底的41块钱降到2019年的26块钱左右。
但当恩捷顶住压力拼命上产能,它的国内同行们在忙于技术路线的切换,而海外对手旭化成、东丽、SKI等,则因成本高、环评难、下游需求不明确等问题,扩产相对谨慎。
相较之下,在2017-2020三年时间中,恩捷通过新建、收购总共获得了40条隔膜产线,到2020年累计产能高达33亿平米。终于,当2020年下半年全球新能源汽车市场销量开始猛增时,恩捷也迎来爆发,当年出货达13亿平米。
恩捷的提前卡位正应了曾毓群的那句“赌性更坚强”,但作为技术密集型的制造业,只会赌是不行的,恩捷在大肆扩张后隔膜毛利率水平仍维持在50%以上的水准,背后还有一套成本控制**。
隔膜的成本中,原材料占到4成,而设备折旧、人工、电费等则占了6成,在几乎所有环节,恩捷都能扮演”价格屠夫“的角色。
在原材料方面,恩捷利用自己的体量优势,以更低的价格采购原材料,并开发回收技术使每条产线的辅料用量下降三分之一[5]。当行业平均原材料成本占收入超过40%时,恩捷将其控制在17%。
在设备方面,恩捷购置的隔膜产线虽然昂贵,但其自身有与设备商联合研发、调试的能力,因此单线设计年产能超过1亿平米,每平米产能固定资产投资仅2元出头,比同行至少低出15%,摊薄了成本的同时,也把产品综合良率做到了78%。[5]

此外,大客户的订单也在其中起到了重要作用。隔膜其实是一个不完全标准化的产品,如果产线频繁在不同客户的产品中切换,每次都需重新调试,耗费数天并产生大量不能使用的残次品。恩捷手握大客户的稳定订单,减少了无谓的消耗。
经多管齐下,尽管国内湿法隔膜(基膜)每平米均价已经从超过10元降低到不足1.5元,但恩捷把每平米成本做到了1元以下[6]。相较而言,国内同行的成本比其高20%乃至更多,而海外对手则可高出100%。
可以发现,恩捷的降本**是一个持续自励的过程:高性价比赢得大订单→大订单带来稳定大规模生产→规模效应反哺,进一步降低原材料采购成本,并提高产品良品率与资本能力(扩产潜力),在这个循环中,恩捷最终铸就了产能与成本双壁垒。
这些壁垒最近还在进一步“自我加固”。11月10日,恩捷宣布将与宁德时代组建合资公司,共同投资80亿新建16亿平米/年湿法隔膜与20亿平米/年干法隔膜产能,新增产能约为恩捷成立以来产能之和。
下一个战场
技术路线的更迭与强有力的成本控制,成就了恩捷,但反过来看,即使强如恩捷,也无法改变“饼干夹心”的宿命。
一方面,在下游电池厂商的压力之下,未来隔膜价格下降的趋势还会继续 ,头部企业也可能沦为“高投入,低回报”的打工仔。面对利润空间的压缩,隔膜企业的普遍应对方式是开拓高溢价的涂覆膜(在隔膜表面涂覆材料以改善性能)与海外市场,从而创造第二增长曲线。
另一方面,隔膜技术路线仍在持续切换中。
2020年开始,磷酸铁锂电池持续回暖,干法隔膜的市场份额扩大了3个百分点。今年因比亚迪刀片电池的放量和特斯拉的力推,磷酸铁锂电池装机量更是多次超过三元锂,干法隔膜隐隐显出要与湿法平分市场的势头。
而各车企与电池企业在积极布局的固态电池,则因采用固态电解质无需隔膜,可能会让整个行业遭遇毁灭性打击。
面对技术路线的不确定性,隔膜大厂的普遍选择是两头同时下注,形成了干湿法龙头相互“偷家”的局面。比如,恩捷与Celgard今年9月合资,建设先进干法隔膜工厂。干法龙头星源材质则积极转向湿法,2020年湿法隔膜产能已达4.7亿平米,超过其干法产能。
对于固态电池可能带来的降维打击,隔膜行业反而表示情绪稳定。由于界面阻抗高、材料成本高等问题,固态电池被认为在2025年前难以规模化量产应用。蔚来将于2022年搭载上车的150kWh固态电池,实际上是半固态电池,其中仍需要隔膜,各家都有布局。
退一步说,电池上能做的薄膜生意不止一种,如果电池内部的隔膜被淘汰,包覆电池的铝塑膜也还有生存空间。
通用、奔驰等企业采用的软包动力电池,需要大量的铝塑膜进行封装,比亚迪据称也将在下一代刀片电池上换装铝塑膜。上海证券预测,2025年全球铝塑膜需求量将达到7.4亿平米,是2020年的三倍,而铝塑膜目前的售价每平米高达20-40元,粗略计算一下,市场规模至少达到180亿元。
因此今年早些时候,恩捷迈出了隔膜企业跨界铝塑膜的最大一步,在常州投资16亿元,计划建设8条铝塑膜产线,产能2.7亿平米。
尾声
和其他锂电材料一样,在下游庞大需求的作用下,中国隔膜产业也走出了一条逆袭之路。
但这场反攻并未完全结束:一方面,国内隔膜企业目前仍主要供应国内电池企业,海外市场仍有很大开拓空间;另一方面,隔膜的原材料高密度聚乙烯目前主要依靠进口,隔膜涂覆的配方与专利主要掌握在国外公司之手,生产线设备同样依赖进口,自行设计、定义、组装出一条隔膜生产线,是恩捷、星源材质等企业都提到的目标。
对中国的隔膜企业来说,下半场才刚开始。
本文来自得或失投稿,不代表66行知号立场,如若转载,请注明出处:https://www.ygx2.com/7/7492.html